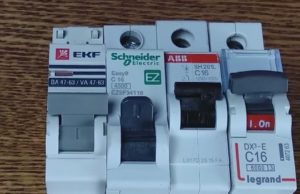
The most extreme mode of operation of the circuit breaker is at the moment of switching off the short circuit current.
The breaking capacity of the machine (the maximum current that the release can turn off) is indicated on the case. But how many such shutdowns this very machine - information - "0" can make.
However, this amount will depend on the strength of the short circuit current. After all, it can be small - 300-400A, or maybe 2000A and 3000A. The consequences will of course be different.
On this occasion, you can find information in GOST R 50345-99 in chapter 9.12.
Household circuit breakers must cope with the short circuit current. up to 1500A at least 9 times, and at currents close to the value of the breaking capacity, but not more than 6000A - 3 times. If I can and agree with the first figure, then with the second on overcurrents ... it seems to me better to replace it with a new one.
Each k.z. creates carbon deposits and scales on the contact area. The contact resistance of such a contact increases markedly and the machine will not be able to work even at rated currents - the contact will heat up and at best the thermal release will work, and at worst ... it can melt the case and even ignite it.
Well ... Today, your attention is invited to see what will happen to the circuit breaker after a series of short circuits.
Test - handicraft, garage. The stand is self-made (each test sample is mounted on a DIN rail). The short-circuit current is created by shorting the wires included in a regular 220V network. No features will be removed. Nevertheless, conditions are created that are close to real. It would be nice to know the short circuit current. networks, at least with the help of such a test. Anyway…
The purpose of the test is a visual assessment of the effects of short circuit current. to the design of the machine.
So, let me introduce the experimental samples:
Do not repeat this test under any circumstances! Mains voltage 220V - life-threatening !!!
The first machine is EKF (the arc chute has already been removed in the photo). Despite its low cost, it did its job remarkably well. The consequences are minimal: there is practically no carbon deposits, scale on the contacts is insignificant.
The second machine is Schneider. Here, to a greater extent, it went to the plastic case - soot is obvious. Contacts have more pronounced dross.
The third machine is ABB. The nature of the damage is the same as in the previous sample.
The fourth machine is Legrand. Relatively good condition of the contacts, the minimum area of soot.
In general, all the machines worked out the money spent on them. However, for further operation, the contacts require stripping. Due to the fact that the hulls are not quickly collapsible, this procedure is not included in their maintenance. In practice, it is unlikely that someone will disassemble the machine to clean the contacts. And it wouldn't hurt!
You can watch the detailed course of the tests in this video: