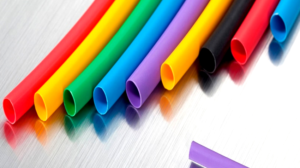
It would seem ... heat shrink tubing for insulating cable / wire connections is no longer something unusual. Someone who, and electricians must definitely know how to use it.
Nevertheless, the other day I watched the work of the RES brigade and realized: “The instructions are not for our brother.” This has been screwed up! (they forgot to put a tube on one of the cores, and during the heating process ... they burned the tubes until bubbles formed). As a result, I have a topic for another article. I hope even experienced electricians will find something useful for themselves.
So…
To begin with, a few words about "what kind of animal it is and what it is eaten with."
The heat-shrinkable tube is designed to insulate the conductive cores of the cable. The principle of operation is simple, “like 3 kopecks”: I pulled it over the place that needs to be insulated, heated it up. The tube decreased in diameter, tightly fixed on the core.
This type of isolation “kills” four “hares” at once:
— reliable dielectric strength (insulation);
- good mechanical strength of the joint;
- excellent moisture protection;
- high installation speed.
And now step by step what you need to do:
- Decide on the length of the tube to be inserted. It should cover the entire non-insulated section of the connection and at least 2-3 cm, “go into” the core insulation on each side. The diameter of the tube should be 20-25% larger than the diameter of the insulated section of the core. This can be done "by eye", or you can ... look at the marking of the tube - it indicates its initial diameter and measure the diameter of the core. Keep in mind that after heat treatment, the tube will decrease in diameter by 2 times!!! Longitudinal shrinkage should not occur, but in fact there is a slight deformation.
- Clean the areas of core insulation adjacent to the connection from dirt.
- The tubes must be put on the cores before they are connected. It would seem that this is an obvious fact, but in the confusion sometimes they forget to do this. As a result, you have to disassemble the connection and mount it again. And do we need it? By the way, RESovtsy, which I mentioned at the beginning of the article, forgot to put a tube on the “zero” core. Then they had to cut the sleeve, pull the tube and sleeve again. In short... extra work :(
- After completing the connection of the cores, move the tube to an uninsulated area. Check that the tube has entered the insulated area on both sides.
- And now the most interesting thing is heating the tube. According to technology, the tube must be heated to a temperature of 120-130 degrees Celsius (this parameter is usually written on the tube itself). But what to warm - the choice is yours:
– or professional equipment (building hair dryer, special thermal gun, gas burner)
- or improvised means (lighter, matches, a regular soldering iron)
In any case, it is important to adhere to the following steps:
- start heating from the middle, evenly heating the tube along the diameter.
- do not heat with movements "from edge to edge", because. with this technology, the formation of air bubbles is possible, and the tube itself will “sit down” unevenly.
- warming up over the entire diameter, it will gradually approach first one edge of the tube, then the other.
Be careful not to overheat the tube - otherwise it will start to bubble and not tightly wrap around the connection.
What not to use.
Some "experts" advise dipping in ... boiling water. I hope you don't follow such a stupid recommendation.
Also, it is advised to seat with an ordinary hair dryer. Whoever recommends this has never done it! Believe me, I have already tried - it does not help! Nozzle outlet temperature too low!
You can use this connection in just a couple of minutes - when it cools down. Good luck to all!