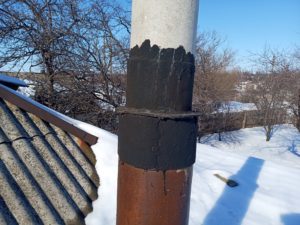
Background.
Since the construction of the stove in my house, an asbestos-cement pipe with an outer diameter of 250mm has been used as a chimney. It consisted of two sections screwed one into one.
The oven is located in the annex. But despite the height of the chimney of 2.5 m, it turned out to be lower than the height of the ridge of the main house. Any stove maker will say that such a scheme will not provide good traction, and moreover, an air jet can be reversed.
So it was. In windy weather, the jet often overturned and the smoke, instead of going up the chimney, went into the house. Partially, this problem was solved by installing the "Fungus" visor on the pipe.
Of course, I understood that the best solution to this problem would be to increase the height of the pipe. But ... somehow the hands did not reach. But the situation itself turned so that I had to do it unscheduled.
As I said, the asbestos-cement pipe consisted of two sections screwed one into the other. So… The upper pipe burst at the junction with the lower one. I had to dismantle it.
There were no similar pipes in any hardware store in the city.
The solution was suggested by a neighbor. He suggested building up with an ordinary asbestos-cement pipe with a diameter of 200 mm. To be honest, I didn't really like this idea:
- firstly, I was afraid that the narrowing of the pipe bore would negatively affect the thrust;
- secondly, there was no idea how to connect two asbestos-cement pipes of different diameters;
Looking ahead a little, I will say right away: the pipe was successfully extended, the thrust ... increased significantly. I forgot about the overturning of the jet, like a terrible dream.
And now the actual technology of connecting pipes.
How to build a chimney.
To connect two pipes of different diameters, I had to make a coupling. The starting material is a steel sheet, 1.5 mm thick.
With the help of a grinder, two rectangles were cut out, 200x630 and 250x790 in size, as well as a circle with a diameter of 300mm with a cut out window with a diameter of 190mm.
Rectangular blanks bent into the shape of a cylinder. I used the appropriate asbestos-cement pipes as a template. The resulting joints are scalded by electric arc welding.
I assembled the structure in this way: I installed a cylinder with a diameter of 250 mm on a flat surface, put a circle with a cut-out window on top, put a cylinder with a diameter of 200 mm on top of the circle.
The whole structure was welded with electric welding.
Pipe installation.
First, the coupling was put on a pipe of a larger diameter. As you can see, looking at the drawings, I left practically no gaps between the pipe and the cylinder. The coupling sat on the pipe very tightly.
Then he inserted a two hundred into the clutch. Due to the tight fit, the pipes are rigidly installed relative to each other.
To avoid possible loosening in windy weather, the top tube is additionally secured with 4 braces.
To prevent precipitation from falling into the pipe, I installed a “fungus” visor.
This design is 2 years old.
Although I was afraid that the narrowing of the flow section would not have the best effect on traction ... I was very pleased with the result of the work: the traction is excellent, there was never a jet reverse, the pipe stands rigidly.